In the workplace, one of your primary responsibilities as an employer is to steer your team clear of operations that come with a high risk of injury. However, when avoidance is not practically feasible, and you need to measure the risk level in order to work out a way forward, it’s important to use risk assessment strategies to minimise the danger to your employees as much as possible.
In this blog post, we’re talking about how you can conduct a proper manual handling risk assessment that will ensure your compliance with manual handling laws and regulations whilst providing practical, easy-to-implement, everyday risk reduction strategies.
Whether it’s moving a box of magazines, lifting a crate of food items onto a higher shelf, or pushing heavy loads around a warehouse, many of us complete manual handling tasks day in and day out. We often don’t think about how we carry out these tasks until it’s too late, and they’ve caused us, or the people we work with, a painful injury.
So, read on to learn more about how to keep your team safe and free from musculoskeletal injuries at work.
Levels of Detail in Risk Assessments
This section will help you understand how detailed your risk assessment should be and what factors you’ll need to consider to keep your team safe.
- Level 1: Simple Filters for Low-Risk Tasks – The first step to a proper risk assessment is to apply simple filters, which help identify low-risk tasks, such as lifting light loads. Some tasks are inherently less dangerous for those involved, and your focus should be on allocating resources to detailed assessments for high-risk jobs. Engaging the workforce in this process not only ensures a more accurate assessment but also creates a workplace culture that sees each member’s involvement in prioritising safety.
- Level 2: Manual Handling Assessment Charts (MAC) or Risk Assessment of Pushing and Pulling (RAPP) Tool – For tasks identified as potentially high-risk, HSE provides specialised tools like the Manual Handling Assessment Chart (MAC) or the Risk Assessment of Pushing and Pulling (RAPP) tool. These tools are designed to zoom in on the most common manual handling risk factors, identifying the actions you need to take to control these kinds of risks more effectively.
- Level 3: Full Risk Assessment – Suppose a detailed assessment has already been conducted using risk assessment tools (MAC or RAPP). In that case, you can improve it with additional information in order to ensure full coverage of all possible risks. Alternatively, a standalone full risk assessment can be undertaken. Depending on the nature of manual handling operations in your workplace, you may not need to undergo all 3 levels of assessment. If you determine a task to be high-risk, you may need to conduct a full risk assessment immediately – be sure to refer to industry-specific guidance.
At OFI, we provide a wide array of manual handling courses to help you create a safe work environment and ensure your staff’s well-being. Dive into our course offerings here.
The Filters: A Lens for Identifying Low-Risk Tasks
Risk filters serve as a lens to identify tasks deemed low risk. If a task aligns with the filter values, a detailed risk assessment may not be immediately necessary. However, exceptions exist, particularly when individual employees may be at significant risk due to specific circumstances. This usually relates to specific demographics of workers, such as new workers, young workers, old workers, or pregnant workers. While the filters draw from scientific literature and practical experience, it’s crucial to underscore that they are not definitive weight limits for safety. Risk filters typically provide guidelines for a reasonable level of safety for around 95% of the population. It is important for employers to recognise groups that do not fall within this category and take additional steps to measure risk levels for them. Manual handling operations, even within the filter boundaries, should be avoided or made less demanding whenever reasonably practicable. For specific filter values, refer to HSE’s guide on risk filters.
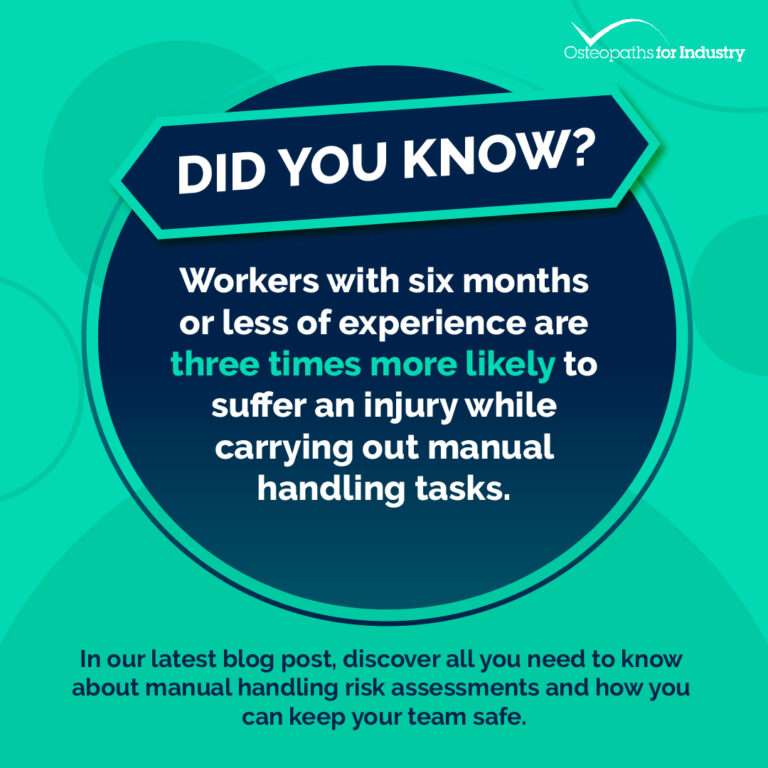
Knowing When to Dive Deeper: When a More Detailed Assessment is Needed
Several conditions signal the need for a more detailed assessment, including:
- Lifting or lowering activities that take place at extreme heights.
- Handling frequencies exceeding one lift every two minutes.
- Involvement of torso twisting, team handling, or complex activities.
- Loads which are difficult to grip properly.
- Unfavourable working conditions.
- Loads which are difficult or impossible to hold against the body.
In such scenarios, it’s vital to prioritise operations that are deemed high-risk for detailed assessments and the subsequent implementation of risk-reduction measures.
In Summary
Properly conducting manual handling risk assessments involves a systematic application of filters, including specialised tools like MAC or RAPP, and, when necessary, a comprehensive standalone risk assessment. This is essential, not only for regulatory compliance but also for empowering you to make strategic decisions that align risk assessment processes with the varied and organisation-specific demands of your manual handling operations.
The overarching goal is, of course, to create a safe and secure working environment for all, where risks are quickly identified and proactively dealt with before they become embedded issues that frequently cause your team members harm. Remember, workplace safety is all about collective effort. You can contact our experts at OFI for more support, information, and safety training solutions, which will keep your organisation productive and ready to thrive.