Tight corridors, flickering lights, and uneven floors can all have highly detrimental effects on employee safety. Indeed, poorly managed workplace conditions often lead to increased risk of injury and illness, so knowing what we can do to improve the safety of our workplaces couldn’t be more essential.
To create a truly secure and supportive workplace, employers must extend their concerns beyond individual tasks to the very environment in which employees work, day in and day out. In this guide, we’re exploring the importance of physical factors in the workplace, including space constraints, floor conditions, temperature, ventilation, and lighting. By understanding the impact these elements can have on how safely manual handling tasks can be carried out, we can safeguard our employees’ physical safety by adopting an approach that takes the whole picture of their daily working lives into account.
Space Constraints and Posture
If your employees’ work environment hinders their ability to work at an comfortable height or maintain good posture, the likelihood of them suffering an injury due to tasks relating to manual handling increases. This is evident in scenarios where:
- Low work surfaces or restricted headroom force workers into a stooping posture.
- Furniture, fixtures, or other obstacles necessitate twisting or leaning.
- Constricted workspaces and narrow gangways pose challenges in manoeuvring bulky loads.
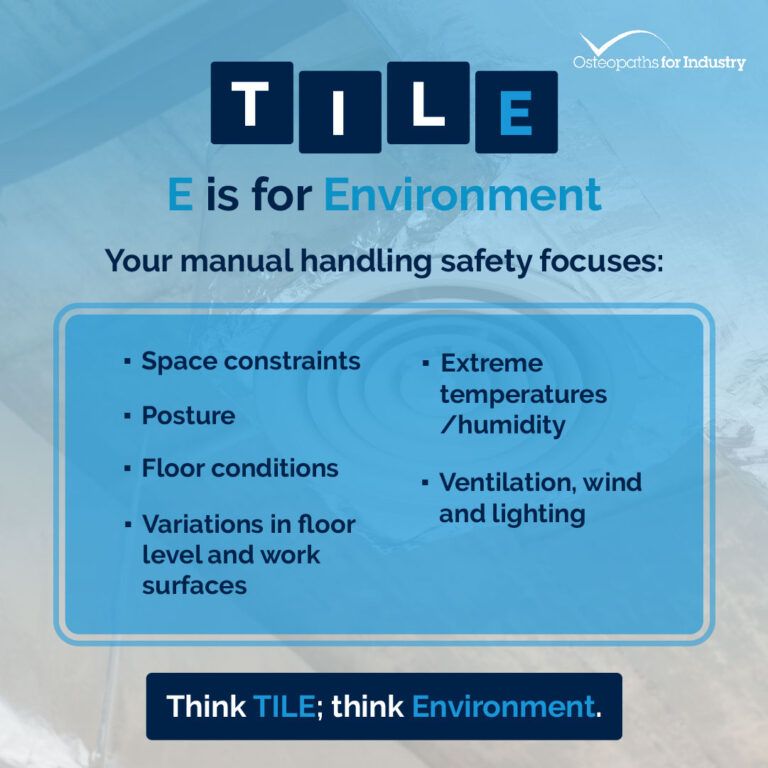
To mitigate these risks:
- Ensure ample clear and well-maintained floor space in areas where handling activities occur, especially around machines, fixtures, and pallets.
- Ensure there is sufficient headroom in gangways and other work areas, preventing workers from carrying or pushing/pulling loads through narrow doorways.
- Ensure there’s enough space for all necessary manoeuvres during manual handling operations.
- Improve organisational standards and housekeeping practices to enhance workspace cleanliness and tidiness and make accidents or injuries much less likely.
Consider incorporating an automatic opening and closing mechanism for doors frequently used during the movement of loads. Keeping some doors open during routine operations can also facilitate easier carrying, eliminating the need for frequent stops and starts, which increase the strain on the body.
Floor Conditions
Irregular surfaces can significantly increase the force required to lift and carry loads, which escalates the risk of slips, trips, and falls. For permanent sites, it is crucial to ensure that surfaces are level, well-maintained, and dry, both indoors and outside. Incorporating slip-resistant surfaces and appropriate footwear can help minimise the risk of slips associated with manual handling. Proper footwear will also reduce the risk of foot injury, as the right shoes can make sure your employees have a stable and supportive base when lifting.
In industries such as construction, agriculture, and sectors where manual handling may occur on uneven or temporary surfaces, proactive measures like ground preparation are crucial. Making efforts to keep the ground even and firm and using suitable coverings where applicable are essential when reducing injury risks.
Uneven or slippery floors introduce challenges to smooth movement, as they add an element of unpredictability to each movement. Furthermore, unstable floors, such as those that move – on a boat, a moving train, or a mobile work platform, for example – also amplify the risk of injury. This can significantly compromise your employees’ ability to handle loads safely, underscoring the importance of carrying out risk assessments before completing tasks and remembering to focus on how the floor conditions might affect safety.
Variations in Floor Level and Work Surfaces
It is advisable to organise tasks on a single level whenever possible to reduce the risk of injury associated with steps and slopes during manual handling activities. Carrying loads on stairs, especially with a two-handed approach, increases the risk of falls by limiting the handler’s visibility, compromising balance, and stopping them from being able to use handrails. When carrying loads on stairs cannot be avoided, consider alternative solutions such as enabling handlers to keep their hands free by giving them a bag or backpack carried on one or both shoulders to carry the load instead. If multiple levels are involved and mechanical devices like lifts or hoists are not feasible, aim to facilitate the transition with a gentle slope or ramp. If that’s impractical, ensure that steps are well-positioned and maintained.
For transferring loads between floors or work levels, plan to use mechanical equipment such as lifts, hoists, or high-reach forklift trucks. Avoid planning transfers via ladders, and if ladders are used for specific tasks, limit the materials and tools carried to lightweight ones, adhering to the manufacturer’s guidelines and risk assessments.
When engaging in pushing and pulling activities, ensure ground surfaces are level, clean, dry, and unbroken to ensure optimal safety for your team. Slopes, if present, should not be excessively steep to ensure adequate control over the load. The force required to push a load up a slope due to gravity increases significantly, emphasising the need for careful consideration of slope angles.
To reduce the risk of injury arising from variations in work surface heights, storage shelving, etc., where possible, aim to maintain uniformity in the height of working surfaces, such as benches, to minimise the need for raising or lowering loads. Alternatively, deploy height-adjustable equipment, such as a scissor lift, to accommodate varying heights and enhance overall workplace safety.
Extreme Temperatures and Humidity
It’s not often we have to deal with very hot weather in the UK. However, it’s important to be aware that engaging in manual handling work under hot conditions elevates the risk of injury, primarily due to the challenges posed by increased sweating and exhaustion. Sweating can pose hazards by impeding vision and making it much more difficult to securely grip loads. In extremely hot environments, this risk only intensifies, especially in high humidity, airless conditions, which can lead to heat stress.
Conversely, low temperatures can impact manual handling work by impairing dexterity, as reduced blood flow to the skin and extremities, like the fingers, becomes a concern. Wind chill can also further decrease working temperatures, impacting employees’ ability to work comfortably and safely. While appropriate clothing can provide insulation against the cold, it can also restrict movement, impair dexterity, and reduce grip. If it’s extremely cold, your workers could also be at risk of hypothermia.
To improve manual handling safety, consider improving environmental control or relocating work areas to avoid extremes of temperature, wind chill, or excessive humidity. In instances where modifying these conditions is impractical, the use of Personal Protective Equipment (PPE) couldn’t be more critical. Conducting a thorough risk assessment in your specific circumstances will help determine whether the work conditions should be classified as ‘extreme.
Ventilation, Wind, and Lighting
Ventilation issues and sudden gusts of wind in enclosed spaces can impact decision-making abilities and induce fatigue among handlers. Sudden gusts of air can also make it much harder to handle large or heavy loads! So, ensuring proper ventilation and protection against gusts of wind is crucial.
Furthermore, inadequate lighting conditions also pose an increased risk of injury. Dimness or glare can make it difficult for handlers to move loads safely. Poorly lit staircases also exacerbate tripping hazards and make it challenging to gauge height and distance. It is essential to ensure your workplace is equipped with effective, well-placed lighting that enables handlers to clearly see their tasks, navigate their surroundings, and make precise assessments of the size, nature, and position of the loads they are handling and how far they will have to move them, in order to reduce this risk. Introducing portable lighting during temporary tasks significantly reduces these risks.
At OFI, we provide risk assessments for your staff or train members of your team to become in-house risk assessors. We can help you preemptively identify risk factors and help you create a safe working environment. We provide expert, in-depth assessments on:
In Summary
Although it’s essential to ensure best manual handling practices are followed in order to prevent your employees from experiencing an injury or developing a musculoskeletal disorder as a result of their work activities, it’s also essential to focus on how the safety of the physical workplace itself can be improved.
Creating a safe workplace must include paying real attention to all the various health and safety considerations within the working environment. You can significantly improve your workforce’s overall well-being and safety during manual handling tasks by addressing space constraints, floor conditions, temperature, ventilation, and lighting. Given the rapidly rising rate of workplace injury, regular assessments, prompt interventions, and adherence to safety regulations must be a priority for employers across the UK.
Wondering how we can help? Don’t forget to explore our services to find out more.